Long-term goals
Focus on your management system
Why should you have an effective quality management system?
- Do you want to ensure long-term customer satisfaction and develop lasting customer relationships?
- Do you want to ensure long-term employee satisfaction and reduce staff turnover in your company?
- Would you like to optimize the quality of your products?
- Would you like to improve your supplier management?
- Do you need recognition by an authority (initial assessment)?
If you want to be economically successful in the long term, it is essential that you structure your company’s processes well and assign the relevant tasks to competent and qualified employees. Recognize risks and opportunities and manage both skillfully!
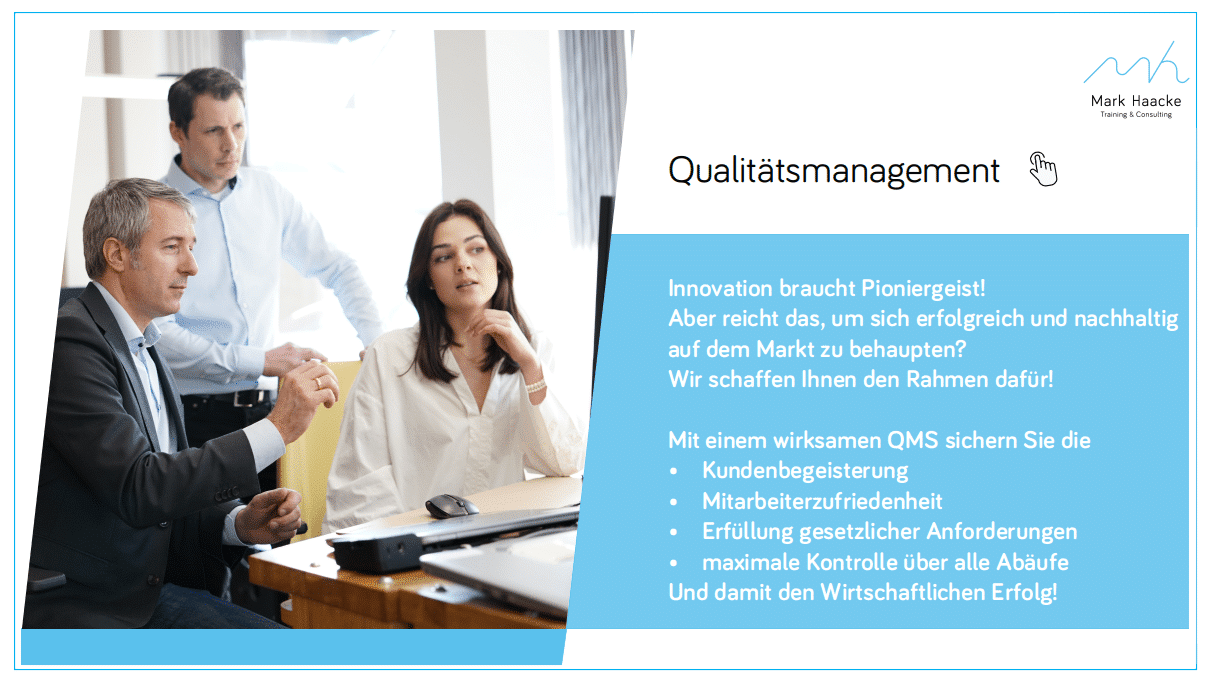
We prepare your company optimally for ISO9001 certification or an initial assessment by a licensing authority. We make sure that you and your employees are not drowning in an abundance of documents and process descriptions, but recognize your quality management system as an important tool and work with it naturally and enthusiastically.
Based on an initial assessment in the form of an internal audit, we work with you to draw up a plan to ensure that you achieve the goals you have set yourself. It makes no difference what products or services you offer. Our support ensures that you achieve your goals.
Legal requirements for your company and your products
Legal requirements apply to all companies and all products – without exception! With solid approval management, you can master this challenge too!
We support you in identifying the relevant standards and show you options on how you can comply with them. Our focus here is on companies with technical and automotive products.
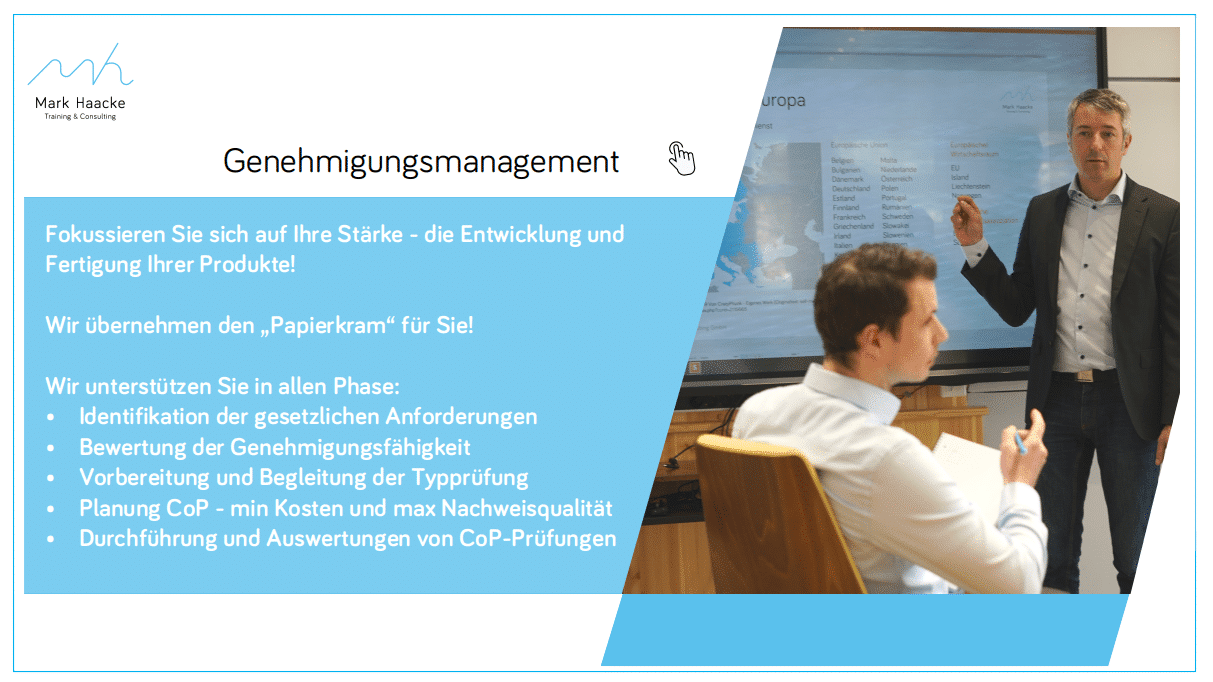
Conformity of Production
However, the legal requirements do not end with a (type) approval!
With the conformity of products (CoP) procedures, you must continuously demonstrate that your products meet the requirements relevant to approval. We support you from the planning stage (CoP inspection plan), through coordination with the authorities, to the implementation and evaluation of CoP inspections.
In addition to our consulting services and interim management, our CoP basic training is very popular.
Non-conformity and hazard
If you have identified or suspect a non-conformity or hazard in your products, we can provide you with full support with our recall management .
Short-term goals
Preparation and follow-up of audits
If you do everything right, you don’t have to prepare an audit! Can you confirm this? Probably not. An audit is always a snapshot and can only check part of the management system.
If you understand audit preparation to mean drawing up an audit plan, defining rules for an audit and informing those involved about the audit date, you are doing everything right.
If you quickly update the date of important (but never used) documents before an audit in order to be prepared for the audit, we should talk about it. We also help you to identify weaknesses in your QMS shortly before an audit and initiate effective measures at short notice. If major or minor deviations are identified during an audit, we support you in the structured development of measures and their implementation.
Support with rejected (type) approvals
You have optimally prepared the approval of your products – from researching the legal requirements to design, prototype construction and type testing. Delivery dates have been planned and supplier components ordered. Now the approval authority is stopping the approval process because requirements have presumably not been met?
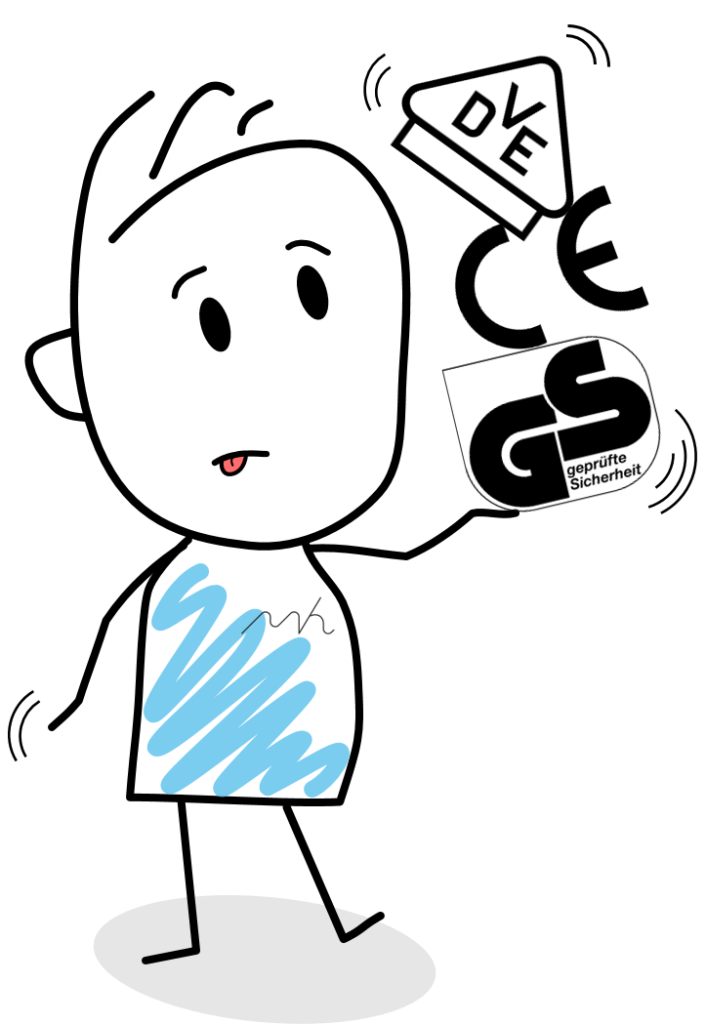
In fact, this is not uncommon. Sometimes requirements were actually overlooked and not fulfilled, sometimes the technical service documented measurements incorrectly, but an incorrect assessment by the authority can also occur.
Are you also in such a situation? Then we can help you quickly and easily! In close cooperation with the authorities and the technical service, we find and analyze the facts and coordinate a satisfactory solution with all parties involved. The aim is to ensure that you can meet your contractual obligations to your customers and minimize the damage caused by a postponed SoP.
Immediate measures in the event of non-compliance and hazards
If you have identified or suspect a non-conformity or hazard in your products, we can provide you with full support with our recall management .
Give us a call or send us a short e-mail. We are here for you!